

Next, I considered replacing only the gear in question, but given it's composition (Zamak, an unweldable and notoriously difficult to repair pressure die-cast Zn/Al/Mg/Cu alloy), I feared that trying to press it out of the assembly would damage the other two pieces (also made from Zamak), making the situation even worse.Īt this point, I figured that trying to repair it in-place was my best-bet-if it didn't work, at worst, I'd either cut off the little gear and make a replacement to fit with what remained of the assembly, or I'd fabricobble a replacement for the whole assembly. As the bed-mounted rack was in perfect shape, I removed the carriage to have a look at the gears behind the apron that mesh with it-sure enough, the 8-tooth drive gear was missing almost an entire tooth.įirst, I tried to find a replacement for the entire carriage-handwheel gear-reduction assembly (two small gears pressed onto a common shaft that passes through a small housing), but didn't have much luck-apparently, this was a frequently broken part, and any remaining back-stock has long since run out. Occasionally, when turning the carriage handwheel, it would slip a fraction of a turn and fail to move the carriage.
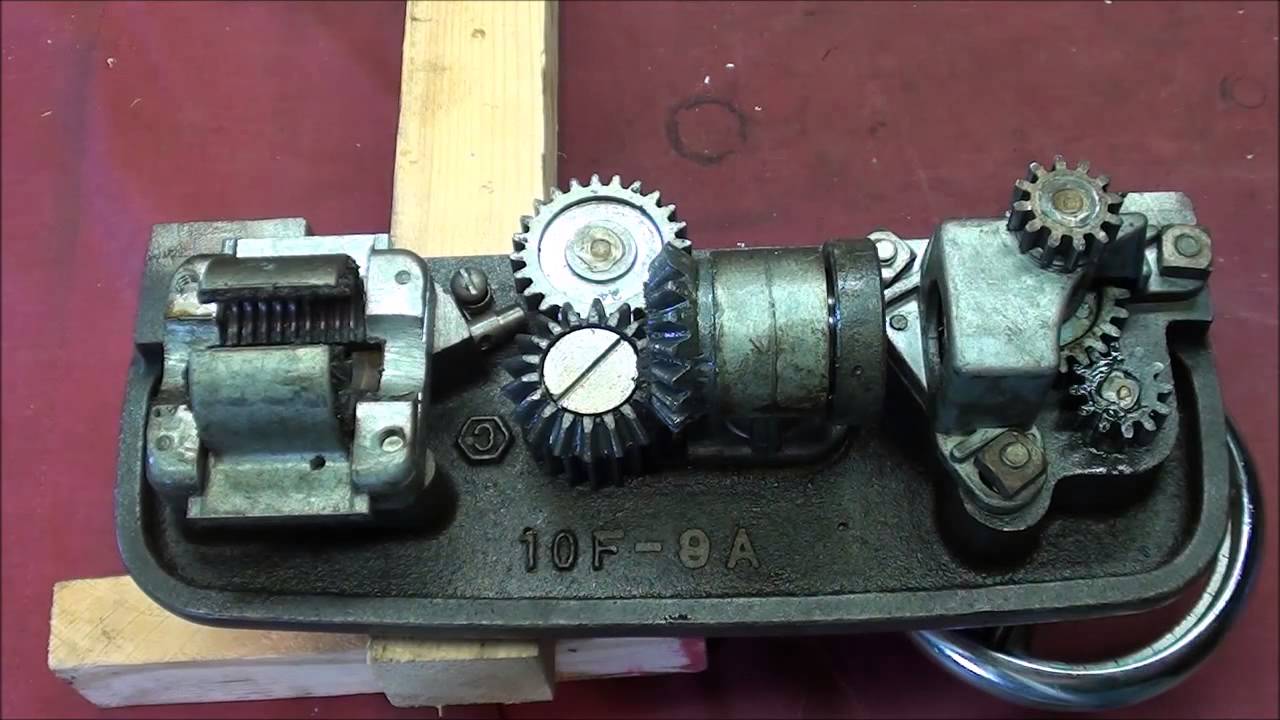
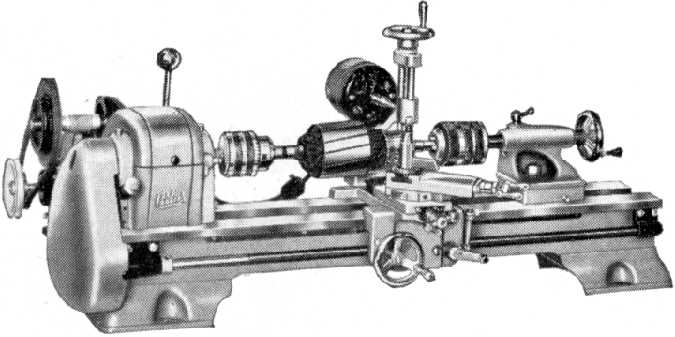
The first problem I noticed was with the carriage handwheel.

These came out well, but while making them, I picked up on a few problems with the lathe that I had initially missed-ones that would need to be fixed before using it for much else.Ĭhuck guard, with aluminum mounting clip made using the lathe milling attachment aluminum mount outlined in lower right for clarity Carriage Drive Gear After making a few accessories, like a butcher-block top to mount it to, some tool organizers and trays for the tooling, and a chuck guard for safety, I finally turned a few parts that weren't destined for use on the lathe itself.
